Since its humble beginnings in 1994 in Halifax, West Yorkshire, Mobus Fabrics has expanded globally and is now a £30 million pound business, supplying upholstery fabrics for some of the world’s leading brands in the furniture industry.
Bringing fabrics to life
With a mission to develop and produce ethically-sourced fabrics that provide value for money, quality and innovation, Mobus is ‘fantastical about fashion and passionate about pattern’, with design-led, fashion-inspired fabrics which appeal to the end user whilst also being fit for intended purposes.
Where it all started
“Myself and our co-founder Mike Presley, set up the company 28 years ago. We were both textile agents, but we saw an opportunity to start Mobus Fabrics with two distinct products that met consumer demand at that time” says Grant. “The first product was called ‘Shabby Chic’, a 100% cotton item, which looked very ‘lived in’ and was very fashionable at the time. The second item was a range of tartan checks.”
It was these two product lines, combined with Grant and Mike’s hard work, that led to Mobus Fabrics turning over £1 million in its first year of business - something that not many new companies achieve in the first 12 months. “It was only supposed to be a weekend job,” says Grant. “But we grew rapidly, and the rest, as they say, is history!”
Developing the business
Until around sixteen years ago, Mobus was commission weaving, coating and dyeing in-house in the UK, buying yarns from Italy and India, but price pressures forced them to look to China for production. “We were still converting our own product, but the UK was rapidly losing its textile infrastructure, so even if we’d have wanted to keep production here, we decided to develop our production business in China in order to remain competitive and meet customer needs,” affirms Grant.
Taking their philosophy from the UK as commission weavers and dyers, Mobus developed their business in China with this same philosophy, continues Grant. “We developed relationships with the local mills, we’d spot a sample and give them clear direction to develop the colours and styles.” Having identified a lack of local fire retardancy processors, Mobus then set up an FR finishing plant in China with two coating lines, and quickly established relationships with retailers such as Next, M&S and John Lewis.
Serious about business
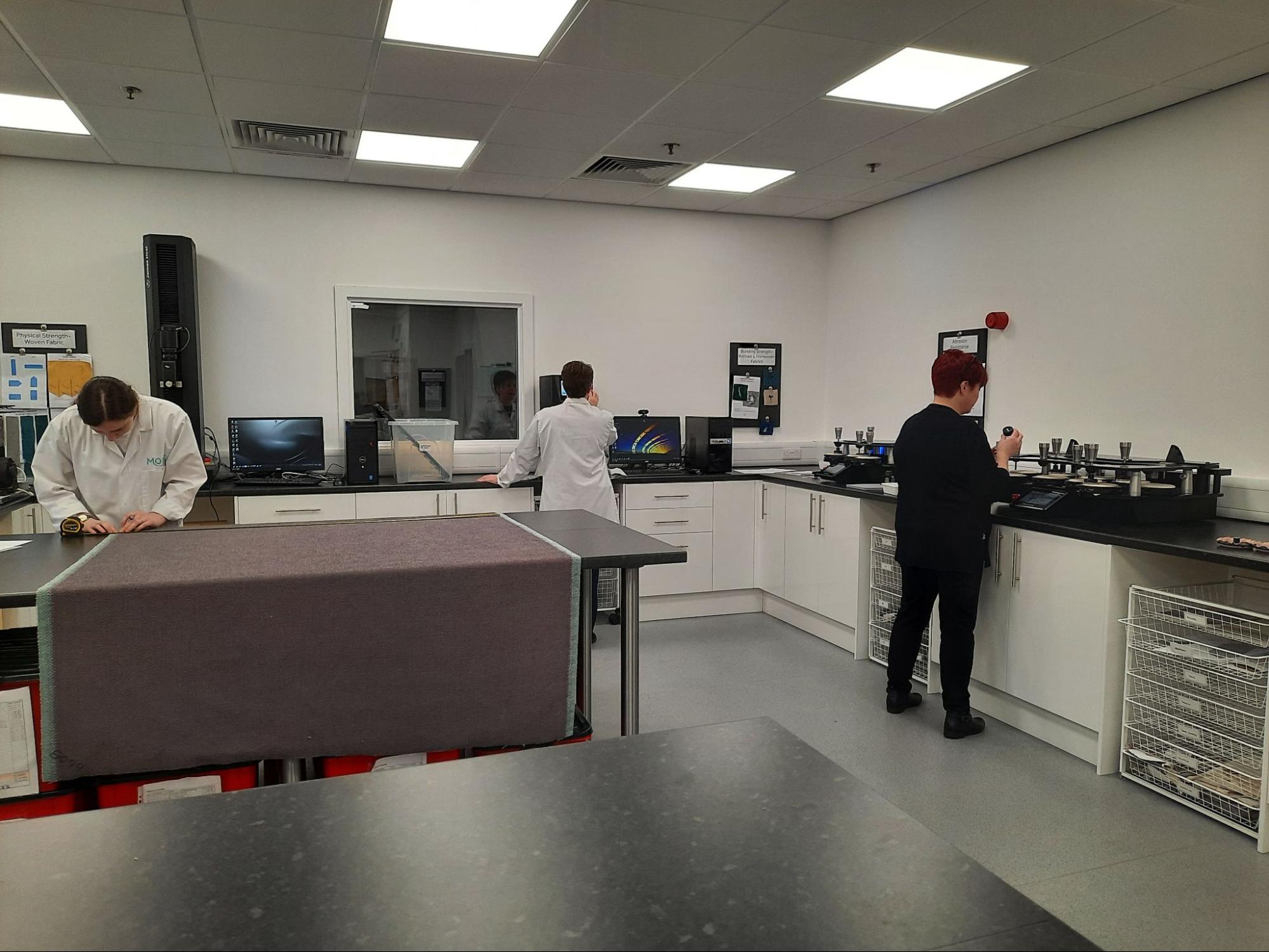
“At Mobus we’ve always taken testing very seriously.” says Charlotte. “Physical testing is the most common type of testing we undertake, where James Heal instruments play a big role. In our internal conditioned laboratory we conduct a full spectrum of physical tests including abrasion resistance; pilling, fuzzing or matting; seam slippage; tear force; tensile strength; bursting strength, and scuffing.”
Mobus' Top 3 James Heal instruments: Titan, Martindale, TruBurst
“We have developed a very good relationship with James Heal over many years,” agrees Grant. “I’ve seen James Heal’s products during my travels in many countries, and it delights me when I see the James Heal brand. It’s recognisable, and for us, it represents quality and a brand who engages with its customers. Not only that, we like the fact that James Heal’s facility is very close to us here in West Yorkshire too, as it makes product training and visits easier”.
Charlotte Beever, Mobus FabricsJames Heal is a forward-thinking brand with a strong customer focus and precision engineering. Their instruments are not only visually appealing in our lab and easy to use, but are built to last. We trust the accuracy and reliability of results, and their service and calibration gives us peace of mind and reassurance.
“While the instruments give us accurate and reliable test results, we do have some challenges with testing to get through,” adds Charlotte. “We find that textile test methods are not always the most realistic representation of ‘real life’ that’s happening in consumers' homes.”
Elaborating on this point, Charlotte says: “A fabric can achieve a required standard, but then its usage and care guidelines can be completely overlooked, meaning that a fabric’s performance and durability fails in real-life.”
Grant agrees, “Nowadays, a sofa is used for multiple purposes in a home - from a seat, to a dining area, to a pet’s bed. Not the intended purpose! Consumers are doing more with fabrics and expectations remain high for a fabric’s durability”.
A solution to this problem is not easy to find either, continues Charlotte, but the key is to "better educate consumers about fabric durability, the importance of after care and ensuring guidelines are read and understood. This could be as simple as improving product labelling at point of sale and highlighting how the fabric should be used in the home."
Importance of in-house laboratory testing
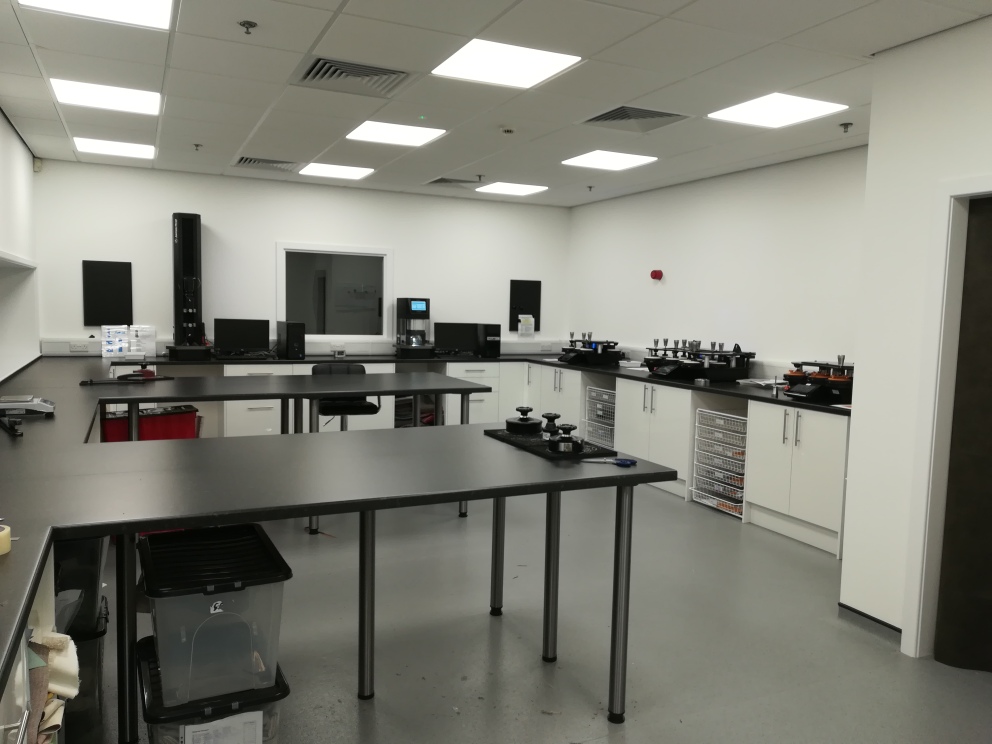
When it comes to making commercial decisions, Grant and Charlotte both agree that having an in-house laboratory is crucial for Mobus. The in-house testing function has grown so significantly since 2014, that it recently became a separate entity, FITT (Furniture Industry Testing Technology) which acts as an independent laboratory servicing Mobus fabrics with a conditioned lab, a wet lab and a flammability lab.
Here, says Charlotte, is where internal testing is used to validate and make more informed commercial decisions about a product, without having to wait for the results of third party testing. “The in-house lab is especially important for our new product development process,” adds Charlotte.
“The fabrics we source go through a rigorous selection process, where they’re tested for performance.” It’s at this stage, confirms Charlotte, that “either the fabric is ‘canned’, or improvements are made, then tested again and colour lines are developed. All the way through, testing is taking place.”
Grant McConnell, Mobus Fabrics“We’ve always believed in quality and ensuring our fabrics are tested to the highest standards. Established in 2014 FITT took over all Mobus testing, and works independently taking a non-biased approach to testing results. Using the latest testing equipment from James Heal, and with an experienced team, FITT has the flexibility to test beyond upholstery guidelines to enable a wider range of tests when required.” -
Focus on green finishing
There’s a new rationale coming from furniture retailers, who want to know their supply chains better, says Grant. “Retailers want to know what chemistry is used, and to make their products more sustainable using less chemicals”.
Grant believes the key to ongoing innovation and product development for Mobus, and indeed the upholstery sector as a whole, is with the finishing, rather than just the fabrics themselves.
“Focusing on finishing gives Mobus a new, and stronger way to differentiate ourselves from competitors,” says Charlotte. “It’s easy for competitors to copy a fabric, even if the fabric has IP protection. But not the finish - which is unique and developed by us”.
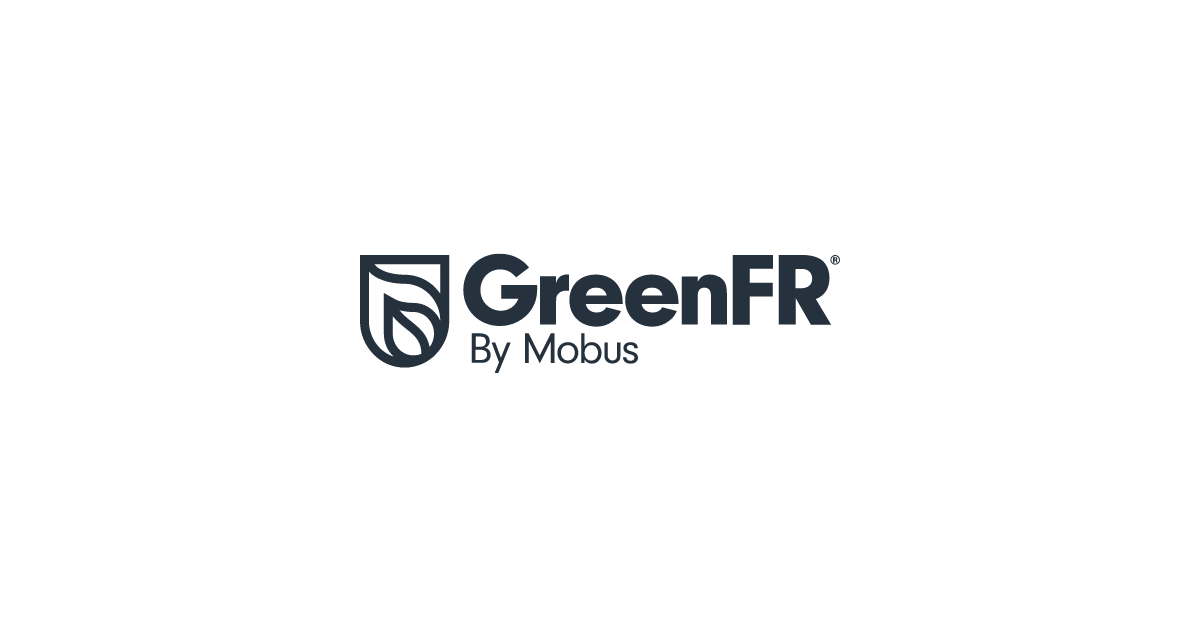
Mobus is developing an innovative GreenFR finish, utilising a halogen-free FR compound - a greener alternative to the deca-brominated FR systems - meaning that when it comes to end of life, there are more options, including delamination of the FR lamination, without a risk of toxic halogen-based chemicals being released. The fabric and furniture materials can then be recycled.
The rationale for this is that cotton and viscose are under more scrutiny, so Mobus is focusing on products they already know and understand, like polyester. However, says Grant “when a solution comes to recycle polyester, current FR chemistry may be problematic in future as it can’t be recycled. This is why we’re focusing our R&D on the finishes rather than fabrics, to find greener, more sustainable finishes to promote recycling at end of life.”
An example of this is global home retailer, Ikea, who have a recycling scheme whereby consumers can return their used furniture to be broken down and recycled. The problem is, the covers are largely polyester-based and therefore not recyclable.
Future outlook
Looking ahead to the future, both Grant and Charlotte agree that the trend for fabrics developed with sustainability in mind will continue to grow, with demand being driven by eco-conscious consumers who have a strong sense of environmental and social values.
“Sustainability is no longer a choice or a desirable add-on for brands in our industry, it’s an absolute imperative,” affirms Charlotte. “That’s why we’re focusing on developing more eco-based fabrics and finishes, such as our green FR finish and the Mobus Eden, our new 100 per cent recycled polyester velvet.”
Grant agrees, “Moving forward, I think we’ll be seeing lots more fabrics designed without chemicals, using more natural dyes and sustainable printing methods.”