As consumers, we may have experienced our white clothing and other fabrics turning yellow at some point. As unsightly as it may seem, this 'yellowing' of white and lightly coloured textiles is a common occurrence, which is usually due to chemical and environmental factors, and fabric ageing.
With around 20% of all textiles produced globally being finished as 'white', it is crucial that manufacturers take the correct precautions to ensure their fabrics and garments stay white during production and storage, so that they reach consumers in the best condition ensuring no financial loss due to rejections and consumer complaints.
What is Phenolic Yellowing?
Phenolic Yellowing, sometimes referred to as Elusive Yellowing, is the discolouration of textiles caused by the action of oxides of nitrogen (NOx) on yellowable phenols, and is a simple, relatively low cost, predictive test to assess the potential of white or pastel-coloured yarns, fabrics or garments to 'yellow' in transit or in storage.
Fibre2Fashion.comAll types of textile products have been subject to yellowing including those made from natural fibers such as cotton wool or silk, as well as those composed of synthetic fibers such as polyester, nylon, or spandex
The 'Phenolic Yellowing Test' was developed by Courtaulds Research, for investigating complaints arising from "storage yellowing". The test is now widely used and is recommended by a number of major retailers, eg Marks & Spencer and Tesco.
It is not intended to deal with the many other causes of discolouration, such as:
- the migration or fading of optical brightening agents
- gas fume fading
- oxidation of fabric lubricants, and so on
However, the Yellowing Test Kit has proved to be an effective means of qualitatively assessing the quality of white and pastel-coloured goods and has considerably reduced the incidence of yellowing complaints.
What causes Phenolic Yellowing?
Yellowing occurs when certain conditions are present while fabrics or garments are being stored.
These conditions are:
- alkaline finishing
- the presence of moisture
- nitrogen dioxide present in the air, and
- storage in polyethylene bags or film containing butylated hydroxytoluene (BHT) or similar compounds
The effects of BHT on white and lightly coloured textiles
The phenolic antioxidant, butylated hydroxytoluene (BHT), was patented in 1947 and received approval for use as a food additive and preservative by the Food and Drug Administration (FDA) in 1954.
BHT is also widely used as an antioxidant in the manufacture of polyethylene films used for packaging. BHT sublimes and migrates easily to items in close proximity.
The results of investigations concerning the yellowing of stored textiles were reported by chemist Kenneth C. Smeltz of Du Pont, at the Atlanta meeting of the American Institute of Chemical Engineers.
As reported in Chemical and Engineering News (March 26, 1984, pg. 27), Smeltz implicated the common antioxidant butylated hydroxytoluene (BHT) and environmental nitrogen oxides in the formation of 2,6-di-tert-butyl-1,4-quinone methide.
The chemistry of BHT
Typically, the fabric or garment is finished by the manufacturer or washed by the launderer in slightly alkaline conditions. It is steamed, covered with a polyethylene wrap or bag containing BHT, and stored in a mill, warehouse, or plant, usually in darkness.
Sara Williams, Technical Specialist - James HealWith time, nitrogen dioxide reacts with BHT released from the bag or film, especially around openings, perforations, or holes, and this reaction causes yellow stains. The compound produced from this reaction, 2,6,2',6'-tetra-tert-butylstilbene-4:4'-quinone, is intensely yellow (often described as canary yellow, or lemon yellow).
How can this be remedied to reduce or stop yellowing?
The remedy is to reduce the NOx level in the air, or use bags not containing the fugitive antioxidant BHT, or finish all white and pastel-coloured goods in slightly acidic conditions.
Many have taken the view that textile finishers should use citric or glycolic acids to finish fabrics to an acidic state. It is unclear whether these would be intended to be washed out at a later date or if they might cause unforeseen problems of their own.
For example, the over use of the non-volatile citric acid on cellulosic fabrics can have detrimental effects on the strength of the fabric and in some cases yellowing, particularly when dried at high temperatures.
Less than 2 ppm of NOx and less than 5 ppm of BHT can give rise to noticeable discolouration under the specific conditions.
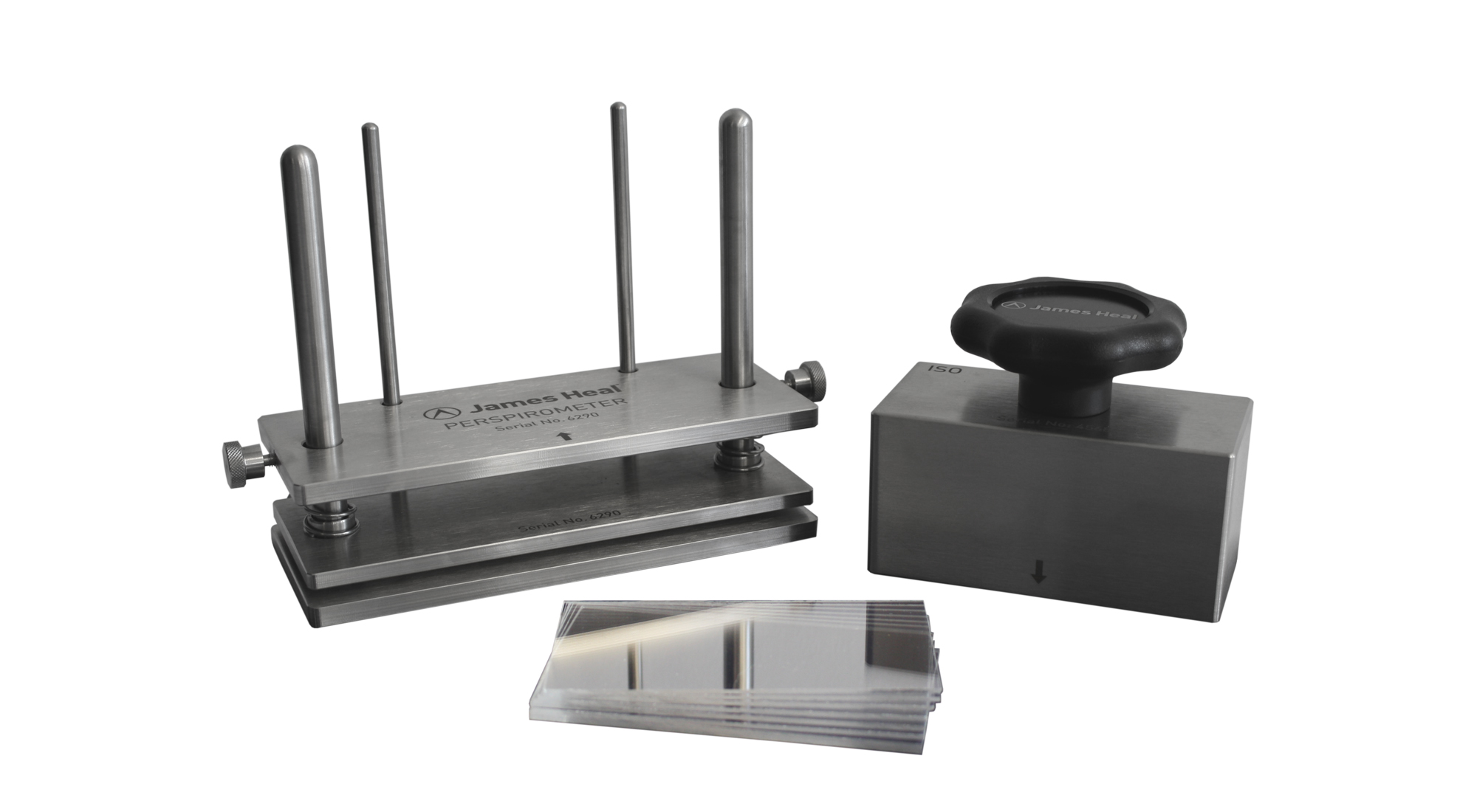
The Phenolic Yellowing test procedure
The risk of phenolic yellowing is evaluated by a 'contact test'. The procedure is based on a 'test paper', which has been mechanically impregnated with a methanol solution containing the phenolic compound.
The test paper is folded along its axis and the specimen to be tested is sandwiched between the two layers.
The sandwich is then placed between two glass plates.
Caution: Do not use acrylic or plastic plates.
A standard test package consists of five test specimens and one control fabric - each separated by a glass plate - making a total of seven glass plates. If there are more than five test specimens, additional test packages are prepared.
Each package is wrapped in BHT-free polythene film. The packages are closed and sealed with ordinary adhesive tape.
To ensure uniform contact between the test papers and the test specimens, the packages are placed in a Perspirometer - up to three test packages in one instrument. The pressure is standardised by the application of a weight. Up to four Perspirometers are placed in an incubator or oven, at a temperature of 50°C ± 3°C.
The treatment time is 16 hours, which permits one day's specimens to be incubated overnight and to be assessed on the following day.
At the end of the test, the Perspirometers are removed from the incubator or oven, the test packages are taken out and are allowed to cool before unwrapping. The specimens are then compared with their originals, and the intensity of yellowing is assessed with a James Heal Grey Scale for Staining (or relative yellowness index values).
How do we know if the test is valid?
The test is considered valid, if the control fabric has turned yellow.
How to store your Yellowing Test Materials
These products are manufactured to provide you with test materials of reliable quality and performance.
In order to maintain this high quality, you should:
- store the products in a cool, dry and dark place
- when not in use, keep the containers and packages firmly and tightly sealed
- once opened, store in cool and dry conditions with container tightly closed, and;
- dispose of after 3 months

What applications and test methods are used for Phenolic Yellowing?
Suitable for use in procedures specified in:
- ISO 105-X18
- M&S C20B
- Tesco TM/137/01
We recently conducted a webinar about how phenolic yellowing happens and how you test for it - watch on-demand now.
Our attendees asked many interesting questions on this subject, which we have compiled on one post.
Subjects include how to recover yellowed garments, treating fabrics in acidic finishes, if gloves can contaminate the test and more.
For more information, check out our Phenolic Yellowing questions and answers (Q&A).
Sources:
- "Update on Yellowing, Vol. 15, Textile Institute"
- "ISO 105-X18, International Standards Organisation"
- "Yellowing of Textiles", Fibre2Fashion.com